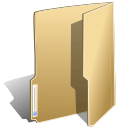
Technical Information (8)
Kurucuların teknik bildiri ve makaleleri:
- YÜKSEK ORANDA UÇUCU KÜL İÇEREN NORMAL VE YÜKSEK DAYANIMLI BETONLARIN KLOR GEÇİRİMLİLİĞİ
- Optimum design of concrete against rapid chloride permeability
- Effects of Fineness and Amount of Fly Ash on Strength Development of Concrete
- Mechanical Behaviour of High Strength Concretes with High-Volume Fly Ash
- STİROPOR HAFİF AGREGALI BETON
MINERAL ADDITIVES
Mineral additives or so-called “Supplementary cementing materials” (SCMs) contribute to the properties of hardened concrete through hydraulic or pozzolanic activity. Typical examples are fly ashes, slag cement (ground, granulated blast-furnace slag), and silica fume. These can be used individually with portland or blended cement or in different combinations. Supplementary cementing materials are often added to concrete to make concrete mixtures more economical, reduce permeability, increase strength, or influence other concrete properties.
Fly ash, the most commonly used pozzolan in concrete, is a by-product of thermal power generating stations. Commercially available fly ash is a finely divided residue that results from the combustion of pulverized coal and is carried from the combustion chamber of the furnace by exhaust gases.
Slag, formerly referred to as ground, granulated blast-furnace slag, is a glassy, granular material formed when molten, iron blast-furnace slag is rapidly chilled - typically by water sprays or immersion in water - and subsequently ground to cement fineness.
Silica fume, also called condensed silica fume or microsilica, is a finely divided residue resulting from the production of elemental silicon or ferro-silicon alloys that is carried from the furnace by the exhaust gases. Silica fume, with or without fly ash or slag, is often used to make high-strength concrete.
Source: cement.org
CONCRETE CHEMICAL ADMIXTURES
Chemical admixtures are the ingredients in concrete other than portland cement, water, and aggregate that are added to the mix immediately before or during mixing. Producers use admixtures primarily to reduce the cost of concrete construction; to modify the properties of hardened concrete; to ensure the quality of concrete during mixing, transporting, placing, and curing; and to overcome certain emergencies during concrete operations.
Successful use of admixtures depends on the use of appropriate methods of batching and concreting. Most admixtures are supplied in ready-to-use liquid form and are added to the concrete at the plant or at the jobsite. Certain admixtures, such as pigments, expansive agents, and pumping aids are used only in extremely small amounts and are usually batched by hand from premeasured containers.
The effectiveness of an admixture depends on several factors including: type and amount of cement, water content, mixing time, slump, and temperatures of the concrete and air. Sometimes, effects similar to those achieved through the addition of admixtures can be achieved by altering the concrete mixture-reducing the water-cement ratio, adding additional cement, using a different type of cement, or changing the aggregate and aggregate gradation.
Admixtures are classed according to function. There are five distinct classes of chemical admixtures: air-entraining, water-reducing, retarding, accelerating, and plasticizers (superplasticizers). All other varieties of admixtures fall into the specialty category whose functions include corrosion inhibition, shrinkage reduction, alkali-silica reactivity reduction, workability enhancement, bonding, damp proofing, and coloring. Air-entraining admixtures, which are used to purposely place microscopic air bubbles into the concrete, are discussed more fully in "Air-Entrained Concrete."
Water-reducing admixtures usually reduce the required water content for a concrete mixture by about 5 to 10 percent. Consequently, concrete containing a water-reducing admixture needs less water to reach a required slump than untreated concrete. The treated concrete can have a lower water-cement ratio. This usually indicates that a higher strength concrete can be produced without increasing the amount of cement. Recent advancements in admixture technology have led to the development of mid-range water reducers. These admixtures reduce water content by at least 8 percent and tend to be more stable over a wider range of temperatures. Mid-range water reducers provide more consistent setting times than standard water reducers.
Retarding admixtures, which slow the setting rate of concrete, are used to counteract the accelerating effect of hot weather on concrete setting. High temperatures often cause an increased rate of hardening which makes placing and finishing difficult. Retarders keep concrete workable during placement and delay the initial set of concrete. Most retarders also function as water reducers and may entrain some air in concrete.
Accelerating admixtures increase the rate of early strength development, reduce the time required for proper curing and protection, and speed up the start of finishing operations. Accelerating admixtures are especially useful for modifying the properties of concrete in cold weather.
Superplasticizers, also known as plasticizers or high-range water reducers (HRWR), reduce water content by 12 to 30 percent and can be added to concrete with a low-to-normal slump and water-cement ratio to make high-slump flowing concrete. Flowing concrete is a highly fluid but workable concrete that can be placed with little or no vibration or compaction. The effect of superplasticizers lasts only 30 to 60 minutes, depending on the brand and dosage rate, and is followed by a rapid loss in workability. As a result of the slump loss, superplasticizers are usually added to concrete at the jobsite.
Corrosion-inhibiting admixtures fall into the specialty admixture category and are used to slow corrosion of reinforcing steel in concrete. Corrosion inhibitors can be used as a defensive strategy for concrete structures, such as marine facilities, highway bridges, and parking garages, that will be exposed to high concentrations of chloride. Other specialty admixtures include shrinkage-reducing admixtures and alkali-silica reactivity inhibitors. The shrinkage reducers are used to control drying shrinkage and minimize cracking, while ASR inhibitors control durability problems associated with alkali-silica reactivity.
Source: cement.org
TECHNICAL INFORMATION FOR CONCRETE
In its simplest form, concrete is a mixture of paste and aggregates. The paste, composed of portland cement and water, coats the surface of the fine and coarse aggregates. Through a chemical reaction called hydration, the paste hardens and gains strength to form the rock-like mass known as concrete.
Within this process lies the key to a remarkable trait of concrete: it's plastic and malleable when newly mixed, strong and durable when hardened.
Concrete’s durability, strength and relatively low cost make it the backbone of buildings and infrastructure worldwide—houses, schools and hospitals as well as airports, bridges, highways and rail systems. The most-produced material on Earth will only be more in demand as, for example, developing nations become increasingly urban, extreme weather events necessitate more durable building materials and the price of other infrastructure materials continues to rise.
Even construction professionals sometimes incorrectly use the terms cement and concrete interchangeably. Cement is actually an ingredient of concrete. It is the fine powder that, when mixed with water, sand, and gravel or crushed stone (fine and coarse aggregate), forms the rock-like mass known as concrete.
Concrete is produced in four basic forms, each with unique applications and properties.
1.Ready-mixed concrete, far the most common form, accounts for nearly three-fourths of all concrete. It's batched at local plants for delivery in the familiar trucks with revolving drums.
2.Precast concrete products are cast in a factory setting. These products benefit from tight quality control achievable at a production plant. Precast products range from concrete bricks and paving stones to bridge girders, structural components, and wall panels. Concrete masonry another type of manufactured concrete, may be best known for its conventional 8-by-8-by-16-inch block. Today's masonry units can be molded into a wealth of shapes, configurations, colors, and textures to serve an infinite spectrum of building applications and architectural needs.
3.Cement-based materials represent products that defy the label of "concrete," yet share many of its qualities. Conventional materials in this category include mortar, grout, and terrazzo. soil-cement and roller-compacted concrete —"cousins" of concrete—are used for pavements and dams. Other products in this category include flowable fill and cement-treated bases.
4.A new generation of advanced products incorporates fibers and special aggregate to create roofing tiles, shake shingles, lap siding, and countertops.
Source: cement.org
TECHNICAL INFORMATION FOR AGGREGATES
Aggregates are inert granular materials such as sand, gravel, or crushed stone that, along with water and portland cement, are an essential ingredient in concrete.
For a good concrete mix, aggregates need to be clean, hard, strong particles free of absorbed chemicals or coatings of clay and other fine materials that could cause the deterioration of concrete. Aggregates, which account for 60 to 75 percent of the total volume of concrete, are divided into two distinct categories--fine and coarse. Fine aggregates generally consist of natural sand or crushed stone with most particles passing through a 3/8-inch sieve. Coarse aggregates are any particles greater than 0.19 inch, but generally range between 3/8 and 1.5 inches in diameter. Gravels constitute the majority of coarse aggregate used in concrete with crushed stone making up most of the remainder.
Natural gravel and sand are usually dug or dredged from a pit, river, lake, or seabed. Crushed aggregate is produced by crushing quarry rock, boulders, cobbles, or large-size gravel. Recycled concrete is a viable source of aggregate and has been satisfactorily used in granular subbases, soil-cement, and in new concrete.
After harvesting, aggregate is processed: crushed, screened, and washed to obtain proper cleanliness and gradation. If necessary, a benefaction process such as jigging or heavy media separation can be used to upgrade the quality. Once processed, the aggregates are handled and stored to minimize segregation and degradation and prevent contamination.
Aggregates strongly influence concrete's freshly mixed and hardened properties, mixture proportions, and economy. Consequently, selection of aggregates is an important process. Although some variation in aggregate properties is expected, characteristics that are considered include:
•grading
•durability
•particle shape and surface texture
•abrasion and skid resistance
•unit weights and voids
•absorption and surface moisture
Grading refers to the determination of the particle-size distribution for aggregate. Grading limits and maximum aggregate size are specified because these properties affect the amount of aggregate used as well as cement and water requirements, workability, pumpability, and durability of concrete. In general, if the water-cement ratio is chosen correctly, a wide range in grading can be used without a major effect on strength. When gap-graded aggregate are specified, certain particle sizes of aggregate are omitted from the size continuum. Gap-graded aggregate are used to obtain uniform textures in exposed aggregate concrete. Close control of mix proportions is necessary to avoid segregation.
Particle shape and surface texture influence the properties of freshly mixed concrete more than the properties of hardened concrete. Rough-textured, angular, and elongated particles require more water to produce workable concrete than smooth, rounded compact aggregate. Consequently, the cement content must also be increased to maintain the water-cement ratio. Generally, flat and elongated particles are avoided or are limited to about 15 percent by weight of the total aggregate. Unit-weight measures the volume that graded aggregate and the voids between them will occupy in concrete.
The void content between particles affects the amount of cement paste required for the mix. Angular aggregates increase the void content. Larger sizes of well-graded aggregate and improved grading decrease the void content. Absorption and surface moisture of aggregate are measured when selecting aggregate because the internal structure of aggregate is made up of solid material and voids that may or may not contain water. The amount of water in the concrete mixture must be adjusted to include the moisture conditions of the aggregate.
Abrasion and skid resistance of an aggregate are essential when the aggregate is to be used in concrete constantly subject to abrasion as in heavy-duty floors or pavements. Different minerals in the aggregate wear and polish at different rates. Harder aggregate can be selected in highly abrasive conditions to minimize wear.
Source: cement.org
ÇİMENTO
Tanım
Su ile temasında sertleşen ve etrafındaki maddeleri birbirine yapıştırma olanağına sahip maddelere ‘Hidrolik Bağlayıcı’ adı verilmektedir.
Çimento da su ile reaksiyona girerek sertleşen hidrolik bir bağlayıcıdır. Su ve agrega ile birlikte betonu oluşturan en temel malzemelerden birisidir.
Çimento Çeşitleri ve standartlar
Genel çimentoların tip ve özelliklerinin belirlendiği standart TS EN 197-1, Çimentoların uygunluk değerlendirmesi için TS EN 197-2 , Çimentoların deney metotlarını kapsayan TS EN 196 serisidir. (
TS EN 197-1 11.03.2002 Çimento - Bölüm 1: Genel Çimentolar- Bileşim, Özellikler ve Uygunluk Kriterleri
TS EN 197-2 12.02.2002 Çimento - Bölüm 2 : Uygunluk Değerlendirmesi
TS EN 196-1 11.03.2002 Çimento Deney Metotları- Bölüm 1 : Dayanım
TS EN 196-2 11.03.2002 Çimento Deney Metotları- Bölüm 2 : Çimentonun Kimyasal Analizi
TS EN 196-3 11.03.2002 Çimento Deney Metotları- Bölüm 3 : Priz Süresi ve Hacim Genleşme Tayini
TS EN 196-5 11.03.2002 Çimento Deney Metotları- Puzolanik Çimentolarda Puzolanik Özellik Tayini
TS EN 196-6 07.03.2000 Çimento Deney Metotları-Bölüm 6 : İncelik Tayini
TS 23 EN 196-7 22.02.2000 Çimento Deney Metotları- Bölüm 7 : Çimentodan Numune Alma ve Hazırlama Metotları
TS EN 196-21 11.03.2002 Çimento Deney Metotları- Çimentoda Klorür Karbon Dioksit ve Alkali Muhtevası Tayini
EN 197 – 1’de 27 farklı çimento ve bileşenleri tariflenmiştir (Bkz. T2) Bunların dışında özel çimentolar da mevcuttur. TS 10157 Sülfatlara Dayanıklı Çimento, TS 21 Beyaz Portland Çimentosu ve TS 22 Harç Çimentosu EN 197-1 kapsamında değildir.
1.3. EN 197 – 1 Kapsamı
Bu standart, 27 farklı çimentonun ve bileşenlerinin tarifini ve özelliklerini kapsar. Her çimentonun tarifini, 6 dayanım sınıfının bulunduğu aralık içinde, o çimentonun üretimi içinde, o çimentonun üretimi için bileşenlerin katılma oranını ihtiva eder, aynı zamanda 27 farklı çimentonun ve dayanım sınıflarının gerekli mekanik, fiziksel ve kimyasal özelliklerini belirtir ve bu gereklere uygunluğunu değerlendirmek için uygunluk kriterleri ve ilgili kuralları tarif eder. Dayanıklılık için gerekli olan özellikler de verilmiştir.
TS EN 197-1 deki çimento tipleri
Yeni ve Eski Çimento İşaretlerinin Karşılaştırılması
Mekanik Özellikler Tablosu
DAYANIM SINIFI |
BASINÇ DAYANIMI |
|||
2 GÜN |
7 GÜN |
28 GÜN |
||
32,5 N |
_ |
³ 16 |
³ 32,5 |
< 52,5 |
32,5 R |
³ 10 |
_ |
||
42,5 N |
³ 10 |
_ |
³ 42,5 |
< 62,5 |
42,5 R |
³ 20 |
_ |
||
52,5 N |
³ 20 |
_ |
³ 52,5 |
_ |
52,5 R |
³ 30 |
_ |
Fiziksel Özellikler Tablosu
DAYANIM SINIFI |
PRİZ BAŞLAMA (dk) |
GENLEŞME (mm) |
|
32,5 N |
³ 75 |
< 10 |
|
32,5 R |
|||
42,5 N |
³ 60 |
||
42,5 R |
|||
52,5 N |
³ 45 |
||
52,5 R |
TS EN 197-1 Karakteristik Değer Olarak Tanımlanan Gerekli Kimyasal Özellikler
Çimento Sözlüğü
Çimento Hamuru : Çimento ve sudan oluşan karışımdır.
Çimento Harcı : Çimento, su ve kumdan oluşan karışımdır.
Hidratasyon : Çimentonun su ile birleşerek sertleşmesi olayıdır.
Priz süresi : Çimento standartlarında priz süresi, priz başlama ve priz sona erme süreleri olarak ikiye ayrılır.
Priz başlama süresi : Çimento su ile birleştikten sonra, çimento hamurunun katılaşmaya (plastikliğini kaybetmeye) başladığı ana kadar geçen süredir.
Priz sona erme süresi : Çimento su ile birleştikten sonra, çimento hamurunun katılaştığı (sertleşmenin başladığı) ana kadar geçen süredir.
Hidratasyon ısısı : Çimentonun belirli bir sıcaklıkta hidratasyona başlayıp, hidratasyon sonuna kadar açığa çıkardığı ısı miktarıdır. Çimento ile suyun birleşmesi ile başlayan kimyasal reaksiyonlar dışarıya ısı verir. Reaksiyonlar devam ettikçe ısının açığa çıkması da devam eder. Başlangıçta yüksek olan hidratasyon ısısı zamanla azalır.
Simgelerin anlamları :
* 32,5 / 42,5 / 52,5 Sayıları
28 günlük en az basınç dayanımını N/mm2 cinsinden göstermektedir. Bu deney çimento harcı ile yapılır. Deneyde, “standart kum” denilen özel bir kum kullanılır.
* “R” Harfi
Yüksek erken mukavemet özelliğini gösterir. İngilizce “rapid” kelimesinden gelmektedir.
* “N” Harfi
Yüksek erken mukavemet özelliği olmadığını gösterir.
* “A”, “B” ve “C” Harfleri
Kullanılan katkı miktarlarını gösterirler. “A” düşük katkı miktarını, “B” yüksek katkı miktarını, “C” daha yüksek katkı miktarını gösterir.
* “M” Harfi
Kompoze çimentoyu tanımlar.
Özel Çimentolar
Sülfatlara Dayanıklı Çimento - SDÇ 32,5
Sülfata Dayanıklı Çimento, C3A (Trikalsiyum Alüminat) içeriği en çok % 5 olan Portland Çimentosu klinkerinin bir miktar alçı taşı (CaSO4.2H2O) eklenmesiyle öğütülerek elde edilen hidrolik bağlayıcıdır. Bu çimento ayrıca mineral katkı içermez. Bu çimentonun performansını arttırmak için TS 10157’de ayrıca “C4AF+2C3A” (Tetrakalsiyum Alüminaferrit + 2 Trikalsiyum Alüminat) toplamında da bir sınırlama öngörülmektedir. Sözkonusu standarda göre C4AF+2C3A toplamı %25’i aşmamalıdır.
SDÇ 32,5 çimentosuyla yapılan standart harcın 28 günlük basınç dayanımı en az 32,5 N/mm² dir. Bu çimento, Amerikan standardındaki ASTM Tip V karşılığıdır. Zemin alkali sülfatları ve yeraltı suyu sülfatları ile deniz suyu etkisindeki betonlarda kullanılmaktadır. Bu çimentonun kullanılmasıyla, sülfat etkisiyle beton hacminin genişlemesine neden olacak bileşenlerin oluşumu engellenir. Hidratasyon ısısı düşük olduğundan sıcak havadaki beton dökümünde kullanılması yarar sağlar.
Düşük Alkalili Çimento
TİP I – II / L.A. PORTLAND ÇİMENTO /DÜŞÜK ALKALİLİ
ASTM C 150/97 Standardına uygun olarak üretilir. Bu çimento alkali-agrega reaksiyonu riskinin sözkonusu olduğu betonlarda kullanılır.